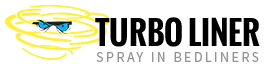
What Is Polyaspartic?
Polyaspartic chemistry was first introduced in the early 1990's making it a relatively new technology. The patents were issued to Bayer in Germany and Miles Corporation in the USA. Pure polyurea reacts extremely quickly making them almost unusable without plural component spray equipment. Polyaspartic technology utilizes a partially blocked amine to react more slowly with the isocyanates and thus produce a modified polyurea. The amine/diamine or even triamine functional coreactant for aliphatic polyisocyanate is typically reacted with a maleate. Polyaspartic esters as they are often called, initially found use in conventional solvent-borne two-component polyurethane coatings.
The reactive groups are the secondary amines. The sterically hindered environment of these groups reduces their reactivity compared to the reaction of typical secondary amines with polyisocyanates. The overall reactivity of the aspartates can be adjusted by changing the “X” group to influence the degree of steric hindrance. In general, the reactivity falls between the very fast curing of a polyurea polymer and the slower reaction rate of a typical polyurethane. The available grades of polyaspartic esters were designed to produce different reaction rates and can be blended to achieve the desired curing profile. The degree of steric hindrance has a limited influence on the film properties of the coating film.
The curing rate of a polyaspartic ester coating is strongly influenced by environmental conditions. As with most systems, the curing rate increases with temperature, but in this instance the rate is also greatly accelerated with increasing humidity. The second generation of polyaspartic ester technology produces formulations that are more robust and show more consistent curing times over a range of humidity levels.